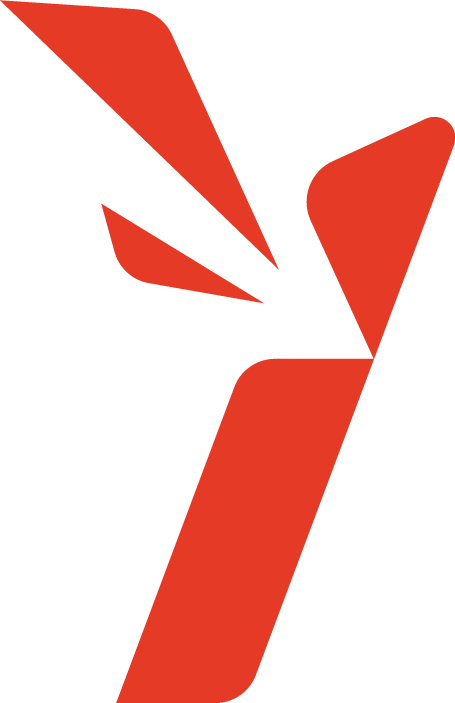
stay up to date
Subscribe to the Ignite Magazine Newsletter
Customer Service, Engineering, Flame Retardants, Process
How to change your flame retardants?: A step-by-step guide for manufacturers
In an industry where safety is paramount, and regulations constantly evolve, updating your flame retardants (FRs) can be complex. At GULEC, we’ve refined this transition process, ensuring your materials comply with the highest fire safety standards and benefit from enhanced overall performance. Join us on a journey from your initial inquiry to delivering a customized FR recipe ready for your production line.
Step 1: Initial Inquiry
Our process begins with a detailed conversation. During our initial consultation, GULEC’s engineers understand your current FR application by discussing the following:
- The types of resins in use.
- Your production methods and critical parameters, such as temperature.
- The fire safety standards and potential regulatory changes affecting your current FR solutions.
- Additional requirements beyond flammability, like UV stability and low-temperature resilience.
Step 2: Determining the Development Roadmap
This phase involves identifying the ideal R&D approach for your FR challenge, typically falling into one of three scenarios:
- 1:1 FR Replacement: Ideally, a direct replacement for your existing FR system is preferred. However, with stricter regulations on halogenated FRs and the differing requirements of non-halogenated alternatives, a 1:1 substitution may be unfeasible.
- Ready-to-Use GERPHOS FR Solution: Our engineers often find a suitable pre-existing GERPHOS solution, which is halogen-free and non-toxic, from our extensive recipe index, significantly reducing implementation time. We then adjust the existing recipe to meet your material’s needs.
- Custom-Made GERPHOS FR Solution: For unique challenges, our team formulates a solution specifically designed for your materials and requirements, demonstrating our cutting-edge chemical engineering innovation.
Step 3: Testing and Fine-Tuning the FR Solution
This phase is where our advanced flame retardant engineering expertise shines. It includes:
- Analytical Phase: Conduct fire tests to analyze your materials’ pyrolysis behavior, focusing on heat release and Real-Time FT-IR observation.
- Simulation Phase: Defining target fire tests and requirements to calculate a starting FR formulation.
- Testing Phase: Rigorously test the proposed FR solution and fine-tune it to ensure seamless integration into your polymer matrix.
Our GERPHOS flame retardants are precisely adjusted for each application, balancing cost-efficiency with enhancing your material’s properties, ensuring compliance and improved performance.
Step 4: Delivery and Validation of a Production-Ready Recipe
Once we finish testing our proposed flame retardant solution we let you test its practical application and effectiveness in your small scale production setup.
- Lab Sample Delivery: We provide initial GERPHOS FR lab samples for client evaluation.
- Client Production of Lab Samples: Clients then produce their lab-sized material samples using our FR formulation to test the recipe’s feasibility.
- Testing and Analysis: Rigorous testing of these samples assesses the efficacy of our FR solution. GULEC assists with fire tests, while clients typically conduct non-fire tests for a comprehensive evaluation.
- Revision and Optimization: We’re prepared to revise the recipe if any tests indicate adjustments are needed, refining the solution collaboratively to meet all requirements.
Step 5: Upscaling to Industrial Trials
Once the lab size sample testing determines the ideal FR formulation, clients implement the recipe in a full-scale production environment and test its viability under operating conditions. Comprehensive testing confirms the solution’s adherence to safety and performance standards at an industrial level, ensuring a smooth transition from concept to production.
Step 6: Continuous Delivery and Support
After successful implementation to industrial production, GULEC delivers the FR solution and provides ongoing R&D support, including responding to regulatory changes or material adjustments to ensure your FR application performs optimally. We’re committed to being a reliable partner in your ongoing journey, offering expertise and assistance to maintain the highest flame retardancy standards in your products.
Conclusion:
Upgrading to the latest flame retardants is a journey of innovation and adaptation. GULEC is dedicated to guiding you through every step, from initial consultation to final delivery, ensuring you receive a cost-effective, compliant FR solution—partner with us to enhance your products and stay ahead in the future of fire safety.
MORE FROM IGNITE MAGAZINE
First returned rock samples shine a light on the Moon’s ‘dark side’
Soil samples from the far side of the Moon provide clues about the origin of lunar asymmetry and the effects of ‘mega-basin’ impacts on the evolution of rocky planets
Calander, Coating, Hydrolysis Reistance, Waterproof
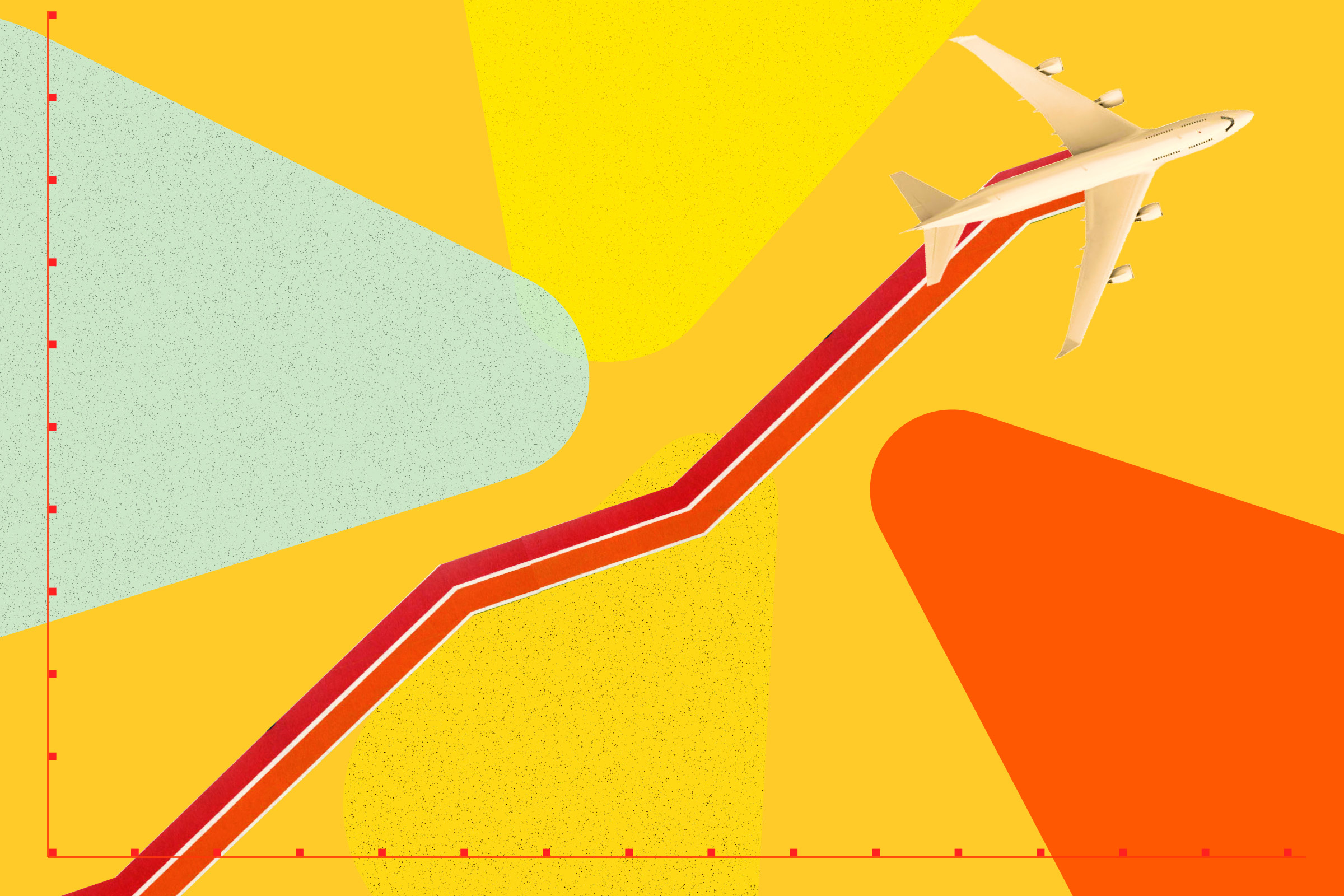
The Antimony Clock Is Ticking
Antimony prices are soaring, and availability is shrinking. If you’re still relying on ATO in your flame retardant formulations, now’s the time to rethink. In this quick update, we outline why switching to halogen-free alternatives like GERPHOS isn’t just safer—it’s smarter.
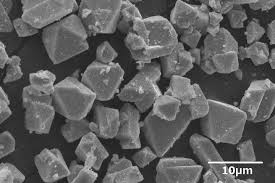